Based in Istanbul and operating with a total of six factories in Tokat Erbaa, we are one of the leading companies in the denim and woven fabric industry, with over 1,700 employees across 60,000 m² of enclosed production space. At Akarteks, we stand out in the industry with our commitment to quality, innovation, and sustainable production, shaping global markets. With our customer-centric approach and state-of-the-art production facilities, we continue to deliver innovative solutions to the denim world.
Production Processes
Model Room
Akarteks Tekstil creates perfect patterns for each product by using the latest software technologies that allow digital pattern correction and design based on brands' custom-sized mannequins. Innovative systems like “CLO® 3D” provide visualization opportunities during the design process, enabling fast and accurate prototype production. This ensures that products are manufactured in the best way, both aesthetically and functionally. Additionally, the specific requests of brands are taken into account during the design and pattern processes, keeping customer satisfaction at the forefront at every stage.
Cutting
In the extensive cutting areas within the facilities, high-precision cutting operations are carried out using state-of-the-art, automation-supported machines. Computer-aided cutting systems minimize fabric waste, contributing to sustainability goals. Cutting processes are continuously monitored through integrated ERP systems to ensure quality, with a strong emphasis on cutting accuracy to ensure products meet exact measurements. Additionally, multi-layer fabric cutting techniques are employed to enhance efficiency.
Laser
Akarteks Tekstil utilizes state-of-the-art laser systems in its production process to create innovative designs and detailed effects on denim and woven products. Laser technology offers an eco-friendly alternative to traditional grinding and distressing methods by minimizing water consumption and reducing chemical use. Applications such as patterns, abrasion, faded effects, and distressing are performed with precision laser machines without damaging the fabric. This ensures that each product is manufactured to meet high aesthetic standards while supporting the concept of sustainable fashion. Products created with Akarteks Tekstil's laser technology stand out with modern design elements and provide innovative solutions to customers.
Embroidery
Akarteks Tekstil enhances products with aesthetic and quality through custom embroidery designs. Using state-of-the-art embroidery machines, detailed and precise stitching is carried out, with every step meticulously planned, from thread selection to stitching techniques. During the production process, logos, patterns, and custom motifs that reflect the unique identity of brands are crafted with the finest details. High-precision computerized embroidery machines deliver symmetrical and flawless designs, ensuring perfection in every product. Akarteks Tekstil combines traditional craftsmanship details with modern production technologies, offering customers both classic and innovative embroidery designs. In line with its eco-friendly production approach, recyclable threads and sustainable materials are preferred, adopting a nature-conscious approach even in embroidery processes.
Sewing
The sewing lines in a total of 6 production facilities are managed by expert teams, ensuring that every product is completed flawlessly. Advanced sewing technologies and processes enhance production speed while maintaining high-quality standards. Each line is optimized for different product types and designs, providing flexibility. Additionally, employees' competencies are enhanced through regular training, ensuring adherence to high standards at every stage of sewing. The durability and appearance of the products are continuously monitored through detailed inspections.
Washing
With its sustainability-focused approach, Akarteks Tekstil has integrated eco-friendly systems into its production processes. Waterless washing technologies and ozone machines significantly reduce energy and water consumption while enabling innovative designs required by denim washing trends. Laser and chemical applications used in washing processes provide precise and environmentally friendly solutions. Each product undergoes multiple tests during the quality control phase after washing, ensuring perfection before reaching customers.
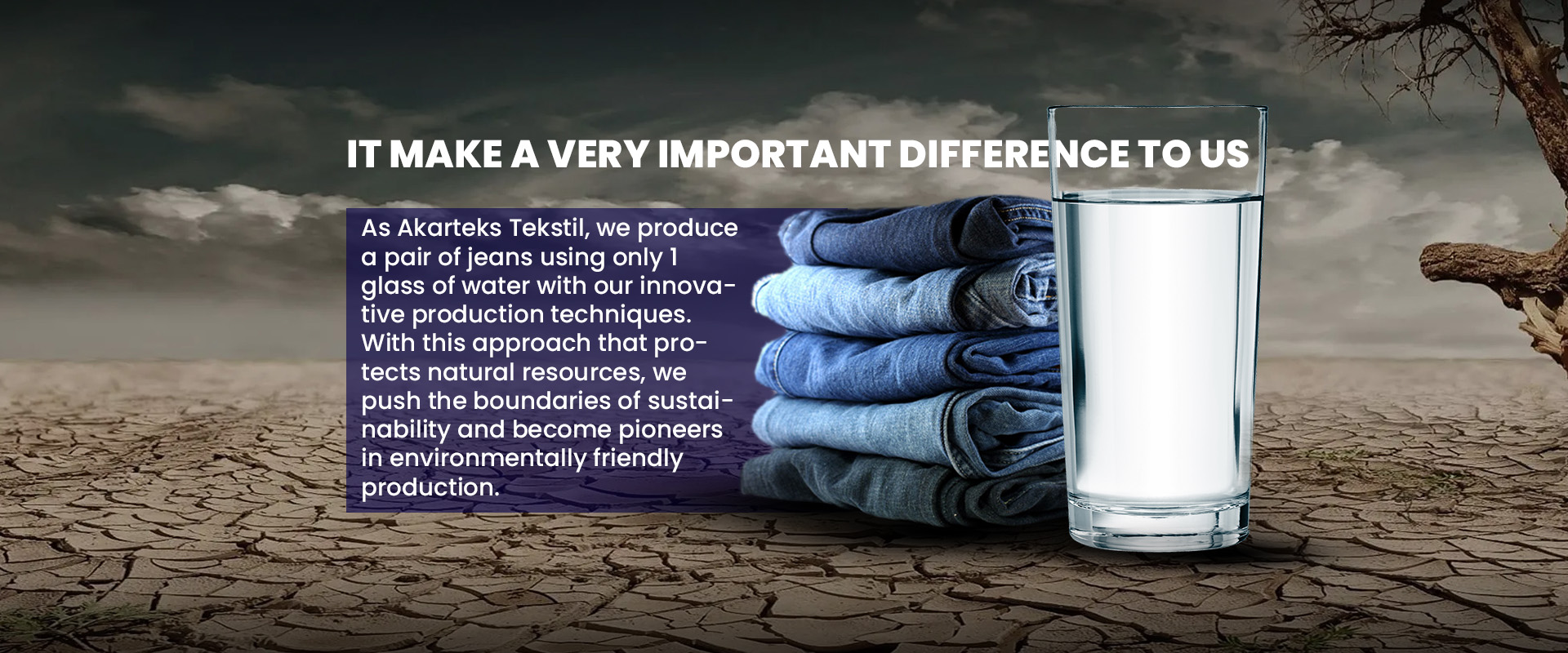
Ironing
After 100% inspection of the products, detailed ironing processes are carried out in accordance with the texture and design of each piece. Thanks to advanced ironing machines and steam systems, the natural structure of the fabric is preserved, wrinkles are removed, and the products achieve their best form. During the ironing phase, temperature and pressure settings are meticulously applied according to the type of fabric to prevent deformation. Special techniques are used, particularly for denim and woven products, to achieve a long-lasting and durable form. Each product is ironed in compliance with international quality standards and prepared for shipment.
Packaging
Products that go through the ironing process are carefully packaged after detailed quality checks. High-quality packaging materials are used to ensure that the products remain in perfect visual and physical condition. Depending on customer requests and logistical requirements, different methods such as folding, hanging, or vacuum packaging are applied. Each product undergoes special protective measures to prevent damage during shipment. Packaging techniques that provide resistance to moisture, dust, and physical damage ensure that the products reach the end user in their original quality. Akarteks Tekstil also prioritizes sustainability in the packaging process by using recyclable and eco-friendly packaging materials.